
No.6 THE ANATOMY OF A SAMPLING CONNECTION JULY 1975 - Revised February 1996)
It happened AGAIN!!! Why is it that people don't read our installation instructions before
they install our sampling kits? The purpose of a sampling probe and some expensive
stainless steel parts with a quick disconnect is to insure that a filter membrane test will be
run on fuel as It flows through the pipe. The oil companies, airlines, the military and
fueling contractors know from experience that you cannot run a meaningful test on fuel
that is stagnated in a branch connection. Why is it that someone hires a contractor with no
aviation fuel experience who installs a sampling probe so it will test the fuel in a DIRT
TRAP?
I once visited an airport fuel farm where I found the exact situation described above. An airline had specified our Kit No. 1 (See Figure 1). All of the parts were assembled correctly but the probe was at least 6" away from the flow stream because it had been located in an unused branch of an 8" pipe tee. Over $600.00 had been spent on at least one occasion to replace the elements in the filter separator because the dirt particles on the filter membrane led the operating personnel to believe that something was wrong. And please don't argue that they must not have flushed properly before running the test! In such a situation, you might have to flush hundreds of gallons before the fuel in a branch connection becomes representative of the main flow stream.
The real purpose of our sampling probe is to make sure that the filter membrane test is run on the kind of fuel that is going through the pipe. The probe (See Figure 2) should penetrate through any reducing bushings as well as the coupling that is welded to the pipe.
In the pictured arrangement of Figure 1, the fuel that reaches the membrane never is in contact with carbon steel from the moment it leaves the flow stream. The entire flow path to the membrane is smooth stainless steel and the diameter is small so that a good velocity can be attained during flushing to carry away any residue or trapped particles.
Do you recall the discussion about velocity in GamGram No.4, "Anatomy of a Jet Fuel
Pipe•? Isn't it even more important to be able to flush a sampling connection? This is why
we have been advocating for 35 years that a flushing hose be used before running the
filter membrane test. Every MiniMonitor Kit that has ever been shipped has been
equipped with one so that the flushing velocity will be more than 10 feet per second
instead of about 0.9 feet per second that the li le MiniMonitor flushing valve (or the one
make by Millipore Corp.) permits at 50 psi. See Model GTP-1110 in Bulletin No.3.
DO THIS
Inspect your sampling connections and answer these questions:
-
Is the fi ing located so you can sample the main flow stream?
-
Is the fi ing on the pipe small enough so that you can really flush it clean?
If not, a probe will solve the problem.
3. Is there a collection of carbon steel reducing bushings, elbows or couplings before the fuel can reach that beautiful stainless steel quick disconnect? If so, would you use a rusty old quick disconnect also? Certainly not! Use one of our Sampling Kits.
4. THINK - Do you ever run filter membrane tests on the upstream side of your filter separator so that you can compare results from the downstream test? Wouldn't this be the logical way to satisfy yourself that the elements are actually capable of removing contaminants?
This puts us into one of our favorite philosophies. Can you feel safe just because you found no dirt or water downstream of a filter separator? You should not feel safe! You could have clean, d fuel going into it! What assurance do you have that the filter is actually in good condition? I, for one, feel much happier when a little dirt and water is known to be in the inlet if the downstream tests show that the filter removed the contamination. When I finish a test, I like to be able to pat a filter on its dome and say, "You're doing your job, old friend."
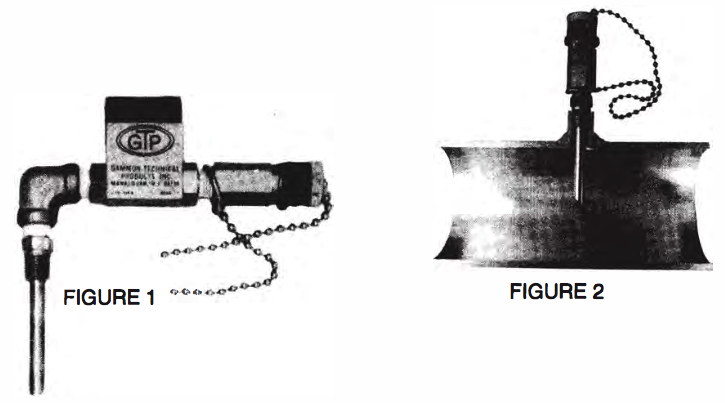
