
No. 50 THE IGNORED AUTOMATIC CONTROL VALVE APRIL 1999
If a valve does its "thing" without any evidence that you can see, people will ignore it and never really learn anything about it. In fact, many operators of aircraft fuel system do not know whether they do or do not have a valve called a rate of flow controller.
So let's begin this article by defining what we are talking about. It is usually called the "rate of flow control" but it is also called by other names that describe its additional functions. For example, a hydrant servicer or refueler truck has a deadman valve but that valve often has multiple functions such as pressure control or flow rate control. In a stationery installation, you may have a slug valve but it may also have other functions such as flow control, pressure control or it may also have a check valve feature. It all depends on whether or not a "rate of flow" pilot valve has been added te the basic valve. We vigorously disagree with the valve manufactures because the name "rate of flow control" is very misleading. The valve goes not "control". It is a "follow rate limiter". It does absolutely nothing until the flow rate tries to exceed the flow rate setting. Then and only then does it do anything. It simply closes just enough to prevent excessive flow.
Did you know that a filter separator cannot be expected to remove water from the fuel without this valve to insure that the flow rate will never be greater than its' design limit? Did you know that the person who specified your valve probably did not specify the flow rate setting? Did you know that the valve manufacturer usually does not ask the customer for the desired flow rate setting? So the chances are that your valve has never been adjusted to limit the flow rate at the correct setting for your filter separator Therefore, it is not only possible that you could operate at a higher flow rate than you do now, but it is also possible that you are operating at a flow rate in excess of your filter separator's maximum rating, with the possibility of water going into the aircraft.
The obvious question is, "How do you test and readjust a rate of flow control pilot valve?" It is really quite simple if there is a meter in the system. There is an adjusting screw (usually under a cap) on the top of the rate of flow pilot valve. (See GamGrams 10, 11 and 12). To increase flow rate, turn the screw clockwise. To decrease flow rate, turn it counterclockwise. Use a stop watch or the second hand of a wristwatch to check the rate of flow on the meter.
If there is no meter in the system, this can be a challenging task, as described below.
HYDRANT SYSTEM - Select a time of day when traffic is very light. Stop flow through all but one filter separator. Coordinate by hand-held radio so that when flow is started, the combined flow rate will be at least as high as the maximum rating of the single filter separator. This may require more than one hydrant ca to be flowing. If the combined rate of flow of the operating gates is different from the rating of the filter separator, make an adjustment and then test again
until you have it right. You then must repeat this process for all of the other filter separators.
TANK FILLING- This is a more time consuming and difficult procedure because the only way
you can measure the flow rate is by checking the tank level rise rate. As a rule-of-thumb, check the tank level over a period of about 15 minutes or a change in level of 6 inches
(150mm), which ever is a greater flow rate. If you do not have an accurate level gauge, we can
offer no advice except to hire someone having a portable ultrasonic flow rate indicator
Very few operators of fuel systems that have 2 or more filters operating in parallel, as in a hydrant system, recognize the fact that each differential pressure gauge will read almost exactly the same if rate of flow control valves are not operating. As an example, consider just two vessels side by side, each with its own differential pressure gauge, as in Sketch A. Regardless of what you do, both gauges will read the same except for differences caused by very small variations in the piping. In fact, the elements could have failed in one vessel or were never installed in the first place, and both gauges would read nearly the same. This is why it is so important to have a rate of flow limiting valve independently adjusted for each vessel as in Sketch B.
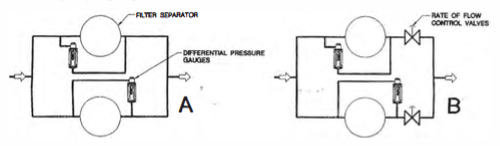
Now that we have covered the necessity of limiting the flow rate, we must remind you that a differential pressure reading means ve little unless you know the flow rate. This was covered in GamGram No. 26, This is the reason we offer the Filter Life Sensor that is described in Bulletin No. 91.
On one of our inspection trips, we had an argument with an engineer who insisted that he did not need flow rate controllers because his system had a separate pump for each filter separator that discharged into a common header. However, when I inspected the installation I found that cross feeding valves were installed so that if a pump or a filter was shut down for maintenance, those valves could be opened. See Sketch C. All of his gauges read the same and this was because all of those valves were left open.
His differential pressure gauges could read accurately only if he kept those cross feed valves closed. Alternatively, if he installed rate of flow control valves at each location marked X, he would also have gauges that read correctly.
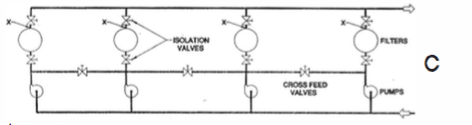
In summary:
1. To insure that a filter separator will remove water, never operate it at a flow rate above its design limit. A "rate of flow control valve" is a necessary piece of equipment.
2. A rate of flow control valve must be adjusted to prevent an excessive flow rate.
3. If a system has 2 or more filter separators in parallel, you will never get correct differential pressure data unless 2 rate of flow control valves are installed.
The valve that is called a "rate of flow controller" is actually a maximum flow limiting valve.
