
No. 44 FILTER SEPARATOR PRESSURE DROP CONTROL DECEMBER 1995
When I was a boy, I heard a story of an event that happened in a nearby town. A large truck (lorry ) got stuck under a low bridge. There was great confusion and no one could figure out how to remove the truck. A young boy kept t ing to get a police officer's attention and the policeman kept telling him to go away. The child was persistent and finally the policeman allowed him to speak his mind. He suggested letting some of the air out of the truck tires and, of course, it worked.
I tell this story because sometimes I feel a bit like that little boy. The message of this GamGram is that there is an inexpensive yet elegant solution to the problem of burst or collapsed elements.
The solution which most people think of first is installation of a differential pressure switch. This works fine, but you also need a control system, test/reset but on and indicator light. Including installation, this can get expensive. To help keep the cost and complexity down, we order a prefabricated system and even retrofit Gammon Gauges. But when you have a control or slug valve already present, there is a better solution.
There are ..slug valves.. on the outlet of most filter separators, and pressure control valves on refueler vehicles. These valves stop flow i water collects in the vessel sump. These are controlled by small pilot valves designed to interact with a float control valve on the filter separator vessel. Frequently, pressure or rate of flow pilots are also included on these valves.
The manufacturers of these slug valves make a little known pilot valve (which can be added) called a Differential Control Pilot Valve. The Differential Control Pilot Valve can sense pressure drop across the filter vessel system and stops flow if pressure drop exceeds a set point (for example - 15 psid). This is one solution, but there is an even better and less expensive solution.
DIFFERENTIAL PRESSURE LIMITING PILOT
Our idea is that you add a "rate of flow" type pilot to your slug control valve. You do this even if you already have a rate of flow control pilot. The new control pilot will not be connected the same way and should be called a Differential Limiting Pilot Valve. Its sense lines are not connected to the orifice plate on the slug valve inlet (as the rate of flow pilot is) but are connected across the vessel itself. (See Figure 1.)
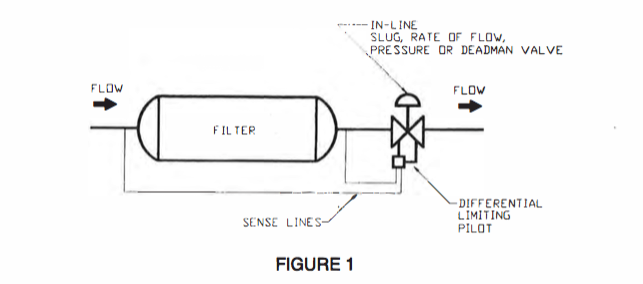
What happens is that when pressure drop is less than your set point (let's say 15 psid) the pilot does nothing. But when pressure drop reaches 15 psid, this pilot starts to close the main valve just enough to maintain 15 psid. The more dirt (or water, in a vessel with water absorbing elements), the lower the flow rate, but you never exceed 15 psid. You lose flow rate, but don't burst the elements. Put simply, you are making the slug valve absorb the pressure drop, not the elements. Even if you are operating at 300 psi, you can't burst the elements.
The beauty of this system is that it allows you to safely continue operation at a reduced flow rate, extending element life and giving you time to get a new set of elements. No other system can do this, and amazingly, it is also the least expensive solution.
Not only can this system be applied to station a filter separators, but it will also work on a refueler truck, as long as an in-line control valve is present. This is especially handy for use on vessels with water absorbing elements or modem fuse monitor elements. It will work with diaphragm or piston type valves.
Well now, GamGrams have always been written in a way to provide information, not to make a sales pitch for our products. This GamGram is definitely aimed at selling, but it's not our product. We are t ing to sell you on requesting this feature on all new vessels. It will insure safer operation of your facility. We have spoken to the valve manufacturers and they will have retro-fit kits available. We would be happy to never hear about burst coalescers and/or collapsed elements again. In addition, you could safely set the pilot up to 20 or 25 psid or more! This really makes be er sense than 15 psid on water absorbing vessels, especially on hydrant trucks. Velcon, for one, is now recommending a 25 psi change out on use type elements. (Check your company policies before changing!)
