
N0. 43 IT IS EASY TO BLAME THE FILTER MAY 1995 (Revised FEB. 2004)
It would be an understatement to say that we are not very happy with the tendency for some people to automatically put the blame on the filter or filter separator for downstream contamination. Frankly, in most cases we have seen, the cause of the problem is the piping design engineer. Recently we have seen some horrible examples that need to be aired. We hope someone is listening; possibly these mistakes will not be repeated.
EXAMPLE NO. 1
Supplying a hydrant system, there is a bank of filter separators and pumps in the fuel farm. The complaint was that the coalescer elements in all of the filter separators had failed. The pleated coalescing media had been bent inward and some pleats were broken. How could this happen when flow is supposed to be from the inside toward the outside? The separator elements were found to have dirt on the inside, but separators flow from the outside toward the inside. How could flow be in reverse?
After a study of the system and the operating practices at this airport, we found that one of the 3 pumps was always on standby. The other 2 pumps came on stream alternately, depending upon demand. See Sketch No. 1. The problem was that the system designer had failed to install check valves in each filter line. When one or two pumps were operating, some flow was recirculating backward through the other pump and filter separator. This reverse flow caused the coalescer elements to fail.
The filter separator failed but the fault was obviously that of the system designer. For little more than $100.00 per branch we solved the problem by adding a check feature to each slug valve. Any brand of slug valve can also be a check valve simply by adding the correct check pilot valves.
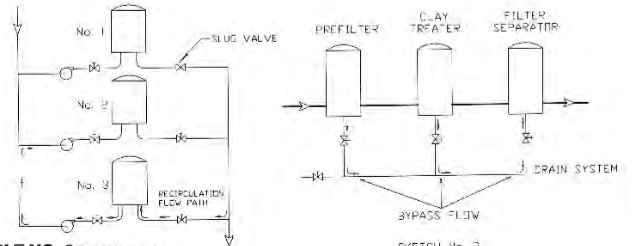
EXAMPLE NO. 2
A major oil company installed a "state of the art" filter system for jet fuel being
delivered to a pipeline that serves a local airport. The system consisted of a
prefilter, clay treater and a filter separator in series.
A work platform was erected so that workmen could change elements without a need to climb ladders.
The system was put in service and the filter membrane colors definitely improved as fuel went through the system but particles began to appear in the effluent. On opening the filter separator, there was a large collection of large particles in the sump but this is the downstream side from the coalescers. Yet, no failure of the coalescers could be found.
It took a while to find the answer. Look at the drain system in Sketch No. 2. Note
that each vessel has its own drain valve but the designer added another shut off
valve as a safety closure at the drain system outlet. We found each vessel drain
valve open but the safety shutoff was closed. Here was the answer. Some of the
flow that entered the prefilter went through the drain system carrying large
particles into the filter separator. The reason the drain valves were left open was
because the workmen found it awkward to crawl under the work platform to
operate them. It was much easier to leave them all open and use the safety shut
off valve when they performed their daily sump drains.
EXAMPLE NO. 3
In their zeal to maintain "closed" fuel systems, piping design engineers are tying systems together in very dangerous ways. In Example No. 2, the drains were tied together. In this third example, the pressure relief valves and the air eliminator discharges for diesel, gasoline, jet and avgas were all tied together. The air eliminators had no outlet check valves. When the avgas system was out of service for a couple of days, diesel fuel that was leaking from a failed pressure relief valve found an easy path into the avgas system, backwards through the avgas air eliminator. The newspapers called it a "filter failure". The press rarely reports things accurately.
We have long urged the use of air eliminator check valves to prevent air from flowing backward into a filter vessel. In this example, a check valve on the air eliminator would have prevented this contamination problem.
EXAMPLE NO. 4
Here is another example of how designers of pipe systems create mammoth problems. In this example, the result was a loss of hundreds of thousands of gallons of jet fuel over a very long period of time at a major international airport. No one could find the reason for the fuel loss.
The installation consisted of over 200 air eliminators, pressure relief valves, low point drains, etc. All were connected to a common waste system with no flow indicators. Of all of these components, there was only one leak and it was from a failed pressure relief valve on a filter separator.
The design error was that there was no way to know when any item was leaking because there were no flow indicators installed. If it had not been for an observant person who heard fuel splashing into the underground collection pipe, the fuel loss might have been much greater.
In conclusion, pipe system designers simply must analyze their work more carefully. If you
absolutely have to tie drains and other pipes together to satisfy anti-pollution and
environmental protection requirements, use flow indicators so that operators can tell if flow is
taking place when it should not, and add check valves to prevent back flow.
1. The Fourth Annual Open House and Trade Show - June 6. An invitation is attached. Please mail us the reservation slip.
2. New Literature: Closed Circuit Sampler - This Aljac product is extensively used in most parts of the world to provide a Clear and Bright check for every refueling operation. It's adoption in the USA is long overdue. See Bulletin 138.
Mini Deadman Handle - Here is a really new approach in electric deadman handle design. Constructed mostly of impact absorbing plastic, its resistance to abuse is excellent. See Bulletin 136.
Mini Monitor Mark II - One of the very first Gammon products was the Mini Monitor Kit for performing filter membrane tests. Now we have made a significant improvement after almost 30 years of successful use. This new model insures uniform color/particle distribution - no more light colored spot in the center of the membrane. See Bulletin 8.
Timer Monitor Deadman System - We did not originate the idea of a fool proof deadman system that requires the operator to re-squeeze the handle periodically. We liked the idea so much, we elected to market a U.S. made system we found that was a major improvement on the original system that came from England. Instead of 4 separate control boxes, ours has just one box. It's a really impressive product. See Bulletin 139.
VISA - MASTERCARD
Yes - we now can accept your credit card for payment in any amount of money up to your assigned limit. Overseas customers have found this capability very useful - no letters of credit needed - we can ship immediately. Military orders also accepted.
