
No. 41 PUMP PRIMING PROBLEMS OCTOBER 1993
Many problems can occur in our industry, but few can be as frustrating as pump priming problems. Many people think that such problems only occur with underground tanks. In reality, priming problems with an above ground, horizontal tank with "top connections" can be even worse. The reason is that air gets trapped in the "high points" in the suction pipe and many pumps (especially centrifugal type pumps) cannot clear out this air. An air eliminator will not solve the problem, because the pipe is NOT under pressure.
It is frustration getting a phone call that starts with "Your pump keeps losing prime". We know pumps can't lose prime. PIPING and VALVES lose prime when fuel drains back into the underground tank. It is difficult for people to understand that pump priming problems are almost always caused by suction pipe leaks.
The most common causes of pump priming problems are, in order of occurrence:
-
1. Leaks in the pipe connections between the floating suction outlet and the roof of the tank.
-
2. Leaks in the pipe connections between the tank and the check valve.
-
3. A leaking check valve (especially if the valve has no rubber seal).
Contractors typically claim that a suction leak is impossible because they "pressure tested the pipe". There are three reasons that they could be wrong.
1. The pipe inside the tank is never properly tested because the test is done before the floating suction assembly is installed.
2. Some pipe sealant compounds slowly dissolve in jet fuel. (Use Teflon tape.)
3. If the pipe was tested with compressed air, a small leak may have been over looked. In addition, some evidence indicates a pressure test may not always reveal a suction leak.
FINDING THE CAUSE
1. Establish flow to a truck, aircraft or another tank, but not back to the tank being tested.
2. Shut the manual valve on the suction line and stop the pump. Have one person listen closely to the open gauging stick opening and ave another person place his ear directly on the pipe as close to tank as possible.
If either person hears bubbling, hissing or splashing, the test is over. If the sound is in the tank, the leak is also. If the sound is in the pipe, the leak could be inside or outside of the tank.
If no sound is heard, wait an hour and start the pump.
A. If the pump primes quickly, wait a minute and stop the pump. Leave the manual valve open. Wait an hour and start the pump again. If it takes a while to prime, your check valve is most likely the problem.
B. If the pump does not prime quickly, go to Step 3.
3. It appears you have a slow suction leak. This must be proven. The tester shown here can be made easily and cheaply. Do not be misled by the lack of high-tech instrumentation; it is the most accurate device of its kind. A 1 psi change causes 3 feet of level change in the tubing.
4. Connect the test device as shown. Cover the pipe with cardboard or other material to shade it from the heat of the sun which will cause thermal expansion and produce a f se result. Close valve "8", and open valve "A". Operate the hand pump until it discharge fuel. Close valve "A" and open valve ''B". Fuel will rise up the plastic tube a distance equal to the vertical distance from the fuel level in the tank to the hand pump. Be sure the ladder is high enough to prevent siphoning.
5. Mark the fuel level on the tube and wait. Very small leaks may cause a drop in fuel level of only 1 every 2-3 hours. Most leaks are more drama c.
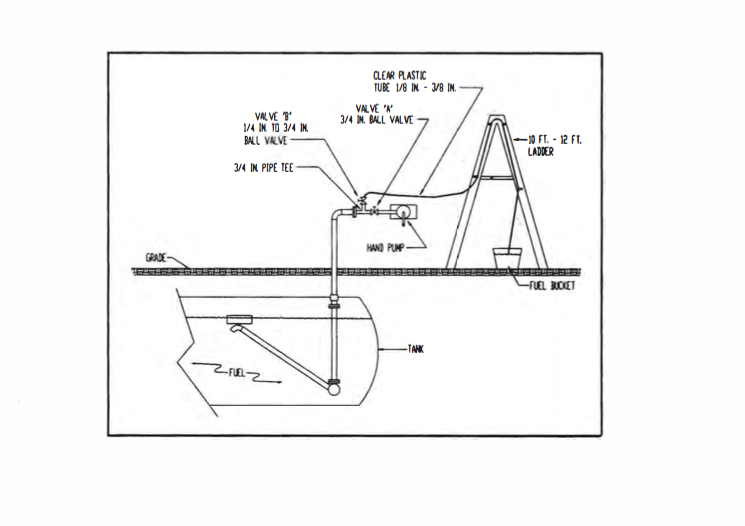
To insure that no leaks are present in the test device, you may wish to coat eve connection with a thick layer of petroleum jelly.
