
No.35 AIRCRAFT FUELING HOSE MARCH 1989
The most abused piece of refueling equipment is the hose. Do people enjoy "beating up" on hose? Or do they do it because it is the only major component that they can kick, bend and generally mistreat without it fighting back? The fact is that aircraft fueling hose is a remarkable product that can take a lot of abuse, but in some respects, it is delicate.
In this GamGram, we are going to point out the astonishing things aircraft fueling hose can do, and we will also tell you how to treat it kindly.
First of all, consider speed. Would you believe that the conventional 300 gpm (U.S.) refueling rate for an airliner means a velocity of 19.2 feet per second (fps)? It's true! That is nearly 3 times faster than the rate we design for steel pipe. And in deck hoses, many operators run at 500 gpm in 3" hose; that is 22.2 fps. The U.S. Air Force packs 600 gpm through 3" hose for a velocity of almost 27 fps. High velocities like this create turbulence that requires exceptional "adhesion". [That is the property that determines how strong the bond is between the inner liner (called the tubel, and the first layer of reinforcing cord]. Poor adhesion results in the tube coming loose and being literally pushed right out of the hose body and into the fuel flow. Is it any wonder that all responsible operators insist on using fully qualified aircraft refueling grade hose, either to API-1529 (American Petroleum Institute) or to the British specification BS-3158?
What about bending? Think of a piece of common rubber tubing having no reinforcing cord in it. Bend it sharply until it is double; it kinks. Let it straighten out, and it will look like new. Bend it again, and it will kink in a different place. Now think about bending a piece of fueling hose until it kinks. (Please use one that has been retired from service). It takes a lot of force, and notice that the cover is smooth and uniform on the outside of the bend, but it has fine ripples on the inside of the bend. Also, there are two points that stick out on opposite sides. (See Figure 1.) When you release the force that caused the kink and let it straighten out, the hose stays out-of-round where it was kinked, sometimes for a long period. It depends on how long the kink is held.
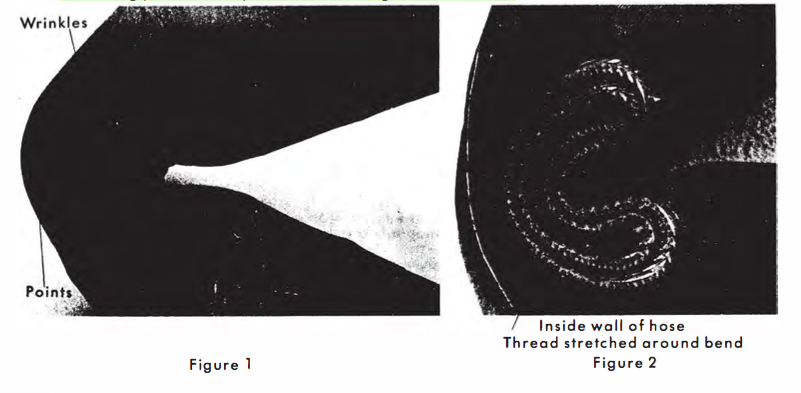
1. If a kink has been held very long, the hose will kink again and again at exactly the same place for the rest of its life.
2. Those two points that are on both sides of the kink are where the hose wall was 'bent absolutely double.
3. Those 2 points are where the hose cover will be worn through very quickly as it is
dragged around on the fueling ramp.
What is the reason that a kink in a reinforce'd hose can become permanent? Rubber
is flexible and it surely straightens out after it is bent. Rubber tubing does not take a permanent kink. The obvious difference is the reinforcing cord in the hose wall. We were puzzled over this phenomenon several years ago, and finally came up with an explanation that no hose expert has been able to knockdown. So here we go!
Consider the cross-section of hose in the photograph, (Figure 2). Now let's consider what is really happening at the bend. The rubber on the outside of the bend (cover) stretches, but the thread will stretch only slightly with respect to the rubber, without taking a permanent set. The rubber that forms the tube of the hose bunches up because it cannot move anywhere. The thread is literally being stretched around the tube rubber. It is overstressed, overstretched and weakened.
Burst tests of kinked hose have not proven that the hose will fail at locations where kinks have occurred once or twice, but it is a well known fact that the hose will be worn through by being dragged on concrete where the kink points are located. However, if the hose has been kinked or a long period, a soft spot develops and bursting can occur.
Just how strong is aircraft refueling hose? The latest specification defines two
grades, 1 and 2. Grade 1 has a working pressure of 150 psi while Grade 2 is rated at 300
psi. The burst ratings are 4 times higher - 600 psi and 1200 psi. These hoses must be pressure tested at 300 psi and 600 psi to conform to the newest industry requirement.
Think of it! The valves and pipe on a refueler truck are tested at only 225 psi which is 1 1/2 times more than design pressure. But the hose is tested at up to 600 psi! Why is this so? In this author's opinion, such a high pressure test is necessary to insure that the couplings are securely attached, but also, because this is the best way to find manufacturing flaws. Tests on used hoses find areas of weakness that have been caused by handling abuse and damage.
The main point we want to leave with you is that hose kinks simply must be prevented. Many times a nozzle storage receptacle will be found in a position such that the hose must be kinked for the nozzle to fit. Sometimes hose reels have fitting connections that force the hose to kink as it winds on the drum. We have seen severe kinks caused by personnel who pull out a hose at high speed. When the last coil of hose comes off the drum, the inertia f the fast turning drum makes it keep right on turning; actually pulling the hose back. This abuse causes the worst kinks we have ever seen. In fact, we have seen small diameter hose broken in this way.
Hose must never be allowed to lie on the ramp with a complete loop. When the hose is pulled, a kink almost alway! occurs, especially if the end that is under the loop is pulled.
With reasonable care, hose can provide reliable service for many years. Abuse by personnel is the greatest single cause of shortened life.
