
No. 31 PIPE, PIPE THREADS AND TUBING DECEMBER 1985
This issue of the GamGram is written out of total frustration. The problem is that it seems necessary for a person to work with tubing, pipe and pipe threads for at least 5 years before he understands them, and then he orders the wrong size fitting half the time.
CUSTOMER COMPLAINING: "I ordered ten (10) 3/8 inch toggle valves, and you sent me these big things with threads that are almost 3/4 inch in diameter".
ANSWER: "Well, 3/8 inch pipe has an O.D. that is just about 3/4 inch-- only 0.075 inches less, so we sent you what you ordered."
CUSTOMER: "But I measured my pipe and it was just about 3/8 inches 0.0 .. How can you say that your 3/4 inch is what I ordered."
ANSWER: "If you had told us what your pipe measured, we would have sent you 1/8 inch valves. Pipe that is 1/8 inch size has an O.D. just 0.03 inches greater than 3/8 inch."
CUSTOMER: "You guys are nuts!"
The customer is frustrated, and so are we. So now we are going to tell you the "facts of life" about pipe sizes. We do not want to appear to justify the peculiarities of the system -- all we will do is explain it. Pipe was originally made by casting processes. The inside diameter measured 3/8 inch or 1 inch or 3 inch, whatever the size was supposed to be. Within the last 120 years, wrought pipe was perfected, but it was found unnecessary to use the heavy wall thicknesses that were required to avoid problems of cast pipe. Wrought materials such as steel and brass could withstand far greater pressures than cast pipe. Obviously, the wall thickness had to be reduced to save metal, but the question was whether the O.D. should be reduced or the I. D. increased. Someone decided that the I. D. should be increased. This way, the wrought pipe could be connected to the same fittings that had been made for cast pipe. This is how the world became confused about pipe sizes.
The following chart gives the sizes of standard schedule 40 pipe. Manufacturing tolerances are not shown. Schedule numbers that are less than 40 or greater than 40 all have the same O.D.; only the I. D. changes. Pipe that is made for high pressures has a thicker wall, and the schedule number is greater than 40, such as 80, 120 or 160. Light duty pipe has thinner walls and smaller schedule numbers, such as 20, 10 or 5.
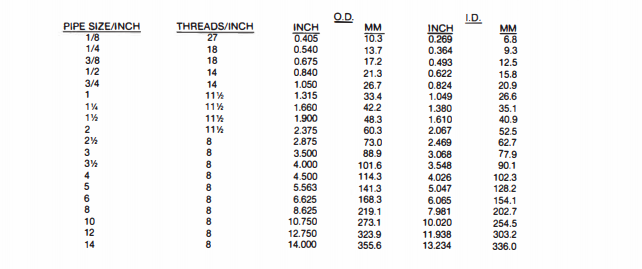
The lesson to learn is that it is impossible to find a dimension on a fitting or a pipe that tells you the actual size until you get up to 14 inch pipe. The O.D. of 14 inch pipe is really 14 inches; the O.D. of 20 inch pipe is 20 inches, etc ..
So now if all of our good customers would please measure their pipe or pipe fittings, our problem will be solved forever-- but we don't really believe that. Why? Because then we develop confusion about tubing sizes.
TUBING
Tubing is measured by its O.D., not its I.D.; 3/8 inch tubing really measures 3/8 inch on its O.D., but its I.D. is usually only about 0.3. Where we have a tubing problem is overseas where metric sizes are used; American fractional inch tubing fittings will not fit. That is why we have to insist that our overseas customers actually take very close measurements. This will insure that we provide the right metric sized tubing fitting.
PIPE THREADS
Most pipe threads in petroleum service outside of North America are straight, not tapered. A gasket does the sealing. When an American product reaches an overseas destination, the mechanic thinks that the fitting should be tightened until no threads can be seen on the pipe. The result is usually that the fitting splits open because of the tremendous forces that are created when two tapered parts are driven together. Regrettably, there is no standard torque that should be used.
Generally speaking, from 4 to 7 turns will produce a tight joint if a thread sealant, such as Teflon tape, is used. Our experience shows that most manufacturers of stainless steel fittings do not adhere to the standards which specify that hand tightness is reached in 4-5 turns. You are lucky to have 2 turns. The number of turns after hand tightening should be 2 or 3.
An exceptionally severe problem develops when stainless steel fittings are screwed into aluminum castings with Teflon tape as the sealant. Although the Teflon provides some lubrication, it is not consistent. If a thread is rough at one point, the Teflon tears away; the mechanic feels the resistance and thinks the joint is tight. It leaks. We have learned over the years that adding petroleum jelly (Vaseline) to the tape after it is applied, makes "all the difference in the world". But we warn you, the very low friction can easily result in a split fitting. Little more than hand tight will make a leakproof connection.
BRITISH PIPE THREADS
Although British tapered pipe threads are used in foreign industry, the petroleum industry in all areas out of North America, seem to have standardized on the British parallel or straight pipe thread. A gasket makes the seal.
We refer to it as BSPP for British Standard Parallel Pipe threads, but we are criticized for adding the second P. The reason we insist on doing it is because BSP can mean either tapered or parallel threads.
The dimensions of BSPP threads are remarkably close to NPT as the chart shows, but the thread form is 55° instead of 60°, and the number of threads per inch is
different. Nevertheless, some mechanics consistently make tight connections with Teflon tape when installing NPT male fittings into female BSPP threads
if one material is soft, like aluminum.
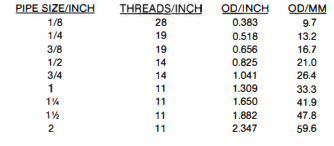
SUMMARY- The only safe way to know what you are doing when you order pipe fittings is to measure with a caliper or a micrometer. We surely do hate to ship parts half way around the world and then find the customer ordered the wrong size.
