
NO. 30 COLD WEATHER OPERATION OF FILTER SEPARATORS APRIL 1985 (Revised JULY 1997)
When an engineer specifies equipment that has little technical foundation, we often call it, "Seat of the pants engineering". This is a perfect description of the way people specify heaters for filter separators. Call it intuition, guesswork, hocus-pocus or pure charlatanism; there really is no apparent technical basis for the way most heater systems are designed for filter separators.
Filter separator salesmen are known to make stupid statements, such as, "A heater keeps the filter separator warm." We recommend that you throw the guy out because he simply does not know what he is talking about. Consider the fact that if your filter separator operates at 600 gpm, and the incoming fuel is at 20°F (-6.°C), the amount of heat required to raise the temperature to 32°F (0°C) is 24,000 BTU/min .. This requires a heat input of 421 KW. Even if you totally ignore the incredibly high heat loss from the vessel surface to the atmosphere, you can easily see that the typical sump heater rated at 1 KW achieves nothing toward heating the vessel. It is like trying to melt steel with a match!
There are really two separate problems in operating filter separators in cold weather:
1. Preventing the vessel drain fitting from freezing. (How can you change elements if you are unable to drain it?)
2. Maintaining fuel flow through elements that are blocked with ice.
The first problem is the most common one. The second problem is restricted to regions where fuel in storage tanks drops well below the freezing point of water.
To keep the drain fitting clear of ice, an immersion heater provides a simple answer, but it takes some careful thought to insure that the heat will be located where it is needed.
Figure 1 is an example of thousands of poorly designed installations. The drain valve is located for operator convenience, but the heater will not prevent freezing at the valve. The design is Figure 2 is good because the drain valve is as close to the heater as possible, and the heater is directly under the drain connection. Convective recirculation up through the drain into the vessel tends to prevent ice formation that might bridge over the drain entrance in the vessel. Heaters rated 300 to 750 watts have been found suitable.
To assist the drain line heater, a sump heater is often used. However, many of them are installed as in Figure 3. Clearly, a heater at this location in the vessel is worthless, because heat will not be located where it is needed, at the drain entrance. In Figure 4, the heater is located so that it can assist the drain line heater in maintaining a clear path for water to leave the vessel. There is no way that the entire deck-plate can be heated, so it must be resolved that ice will exist in areas located away from the inlet of the drain. Obviously, most of the heat from such a heater will rise upward, away from the water that collects, so it is very important that the heater be located as close to the sump surface as possible -- hopefully no more than V2 inch (12mm) above it.
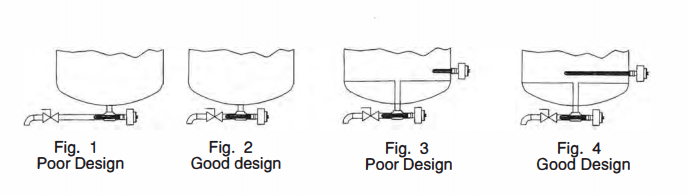
We now return to the problem of dealing with ice that forms in fuel before the water
has settled to the sump. Underground storage tanks almost never have very low
temperatures, except possibly in arctic regions. The fuel in above-ground storage
tanks can drop far below the freezing point in many parts of the world. As the
temperature of fuel drops below the freezing point, water that was dissolved in the
fuel appears as ice crystals in the form of microscopic needles that do not tend to
settle because they are too small. Coalescer elements become hopelessly blocked
by these slivers of ice.
Dealing with this problem is extremely difficult and there are few alternatives. All are very expensive and none are simple:
A. Use anti-icing additives.
B. Install the filter equipment in a heated building. When the elements become plugged with ice, stop the flow and wait until the ice melts. If you have extra money,
install two parallel filter systems so you can switch from one to the other to allow thawing.
C. Heat the fuel storage tank to keep ice from forming.
In case you would like to know some other methods that have been used in the last 40 years, consider these:
1. One filter separator manufacturer had a specially designed unit that you buried in the ground with only the cover exposed. Earth is a great insulator!
2. Hundreds of filter separators were installed inside of plywood boxes having electrical space heaters inside. It was necessary to dismantle the box to change the elements.
3. Hundreds of installations were made with the sump and drain piping thermally insulated (lagged). Rain water always leaked into the insulation making the heating task far worse; many vessels rusted on the outside nearly to the point of structural failure.
We know of two airports that were kept in operation in a recent winter because the ice-blocked coalescer elements were periodically removed and thawed in a heated building. Fueling of aircraft was maintained by alternately using two sets of coalescers. There are no low-cost solutions to this problem.
In conclusion, concentrate on keeping drain systems clear of ice, and then hope and pray that you will not have to deal with wet batches of jet fuel.
