
No. 16 "MICRON" RATINGS MAY 1978 (Revised November 1996)
If you could slice this sheet of paper edgewise into a pile of 75 ultra-thin sheets of paper, each sheet would be one micron (micrometer) thick. The human eye can begin to recognize that a particle is .. in view .. if it is made up of about 400 one-micron particles arranged to fall within a circle that is 1/3 the diameter of a human hair. ARE WE GETTING THE POINT ACROSS? A MICRON IS SUPER SMALL!!
The filter industry is in a terrible state of confusion about rating their filters. To a large extent this is their own fault, but users are customers and they are very demanding creatures. They want things made simple. The micron rating was an attempt to make filtration simple. Unfortunately, it has make liars out of many people and simpletons out of others.
An example of a typical problem is best described by a membrane such as is used to test jet fuel. It is made with a remarkable uniformity - the pores are 0.8 microns in size. Suppose now that you start to flow through the membrane. Almost immediately the pores begin to be partly clogged by particles that are not the same shape as the pores. In a very short time, you note that the flow rate has decreased, it's obvious. Can you still say that the membrane is filtering at 0.8 microns? Certainly not! It's filtering at a much finer level - maybe only 0.3 microns.
THE POINT WE ARE MAKING IS THAT A FILTER HAS ITS MANUFACTURED RATING FOR ONLY A SHORT TIME UNTIL YOUR DIRT BEGINS TO DO SOME OF THE FILTERING.
The trick in making a filter hold a lot of dirt before it plugs up, is to get the particles of your dirt to arrange themselves so that they so not form a film that will stop flow. The membrane described above is a good example of a 111ow dirt holding .. filter. The dirt forms a film. (We are not criticizing the product. Its real purpose is not to be a process filter, but a laboratory tool.)
If we want to increase the dirt holding ability of a filter, we can put a layer of fuzzy material on its inlet face. By skillful arrangement, we can cause the dirt particles to stop in the pre-filtering layers and we can prolong the life of the original filter layer by hundreds of times. Then we can take the sheet and pleat it so that we can multiply the filtering area many times more.
OUR THIRD POINT IS THAT THE TRUE MEASURE OF A FILTER IS HOW MUCH DIRT IT WILL HOLD BEFORE IT PLUGS UP.
To rate the degree of filtration, you need a practical measure. Some people will argue that if one 50-micron particle can find its way through, you must rate the filter at 50 microns. This is the .. ABSOLUTE .. rating "school of thought". The fact that the same filter is probably removing literally millions of 5-micron particles is of no interest to these people.
The obvious impracticality of this method resulted in the "NOMINAL" rating "school of thought". The idea was that if you found that 98% of the particles that were larger than say 10 microns were being stopped by the filter, you should rate it as a 10-micron element. The test is performed using standardized filter test dirts that are carefully graded so that you have a size distribution over a wide range.
Filter manufacturers discovered that a 98% 1 O-micron element could also be rated at 5 microns if you used a lower percentage - say 94%. The same element could even be rated at 1 micron if the percentage was even lower, say 78%. They argued that the true measure of an element is not necessarily how well it removes particles larger than 10 microns but how well it also removes smaller particles that the customer may want to minimize but not necessarily eliminate form his
fluid.
OUR FOURTH POINT IS THAT A FILTER ELEMENT CAN REALLY HAVE MANY MICRON RATINGS AND THERE IS TRULY NO SINGLE RATING THAT TELLS THE WHOLE STORY.
A variety of groups have attempted to improve the communication of filter performance. These include American Institute of Chemical Engineers, American Society for Testing Materials, and National Fire Protection Association. A major step was taken by Oklahoma State University which developed the Multi-pass Test. (Also called the Beta Ratro test). This test addressed the needs of the hydraulic equipment makers but has never been applied to aviation fuel. It introduced the concept of filter evaluation using particle counts. The number and size of particles found in samples before and after the filter were compared throughout the life of the filter. A "beta ratio" (at a specific particle size) and contaminant capacity were then calculated for comparison. The Beta Ratio Test has been upgraded over the years and is now an ISO standard.
Now you are wondering what all of this has to do with jet fuel We have said it many, many times before but here it is again - THERE IS NO MICRON" RATING SPECIFICATION FOR COALESCERS OR FILTER SEPARATORS.
Hardly a day goes by without someone asking us the micron rating of a coalescer element. If we say 1, 2, 5, or any other number, we are simply giving you a relative idea of how different grades of elements perform with respect to one another. There simply is no test or rating procedure required by any agency: API, Military, oil company, airline or FAA.
In their astonishing wisdom, the people who have written specifications for filter separator elements have never called for a micron rating. Instead, they specify a test dirt; then they tell you how much is allowed to pass through the element. This is real wisdom. The most popular test dirt is red iron oxide which has a particle distribution as shown in the following table:
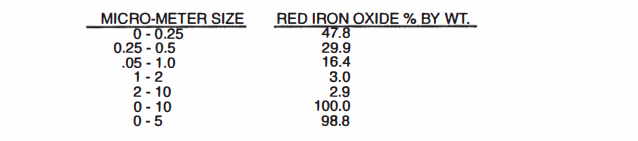
In a typical test, the element is subjected to 1 0 grams per gpm and is allowed to pass 0.001 grams per gallon. Don't you agree that this is more meaningful than a micron rating that never remains constant and never is the same as when the filter was manufactured?
OUR FIFTH POINT: IF YOU WANT TO KNOW HOW YOUR COALESCER ELEMENTS WILL FILTER, ASK THE MANUFACTURER FOR PROOF THAT HE PASSES THE API TESTS. IF HE
DOES, YOU CAN BE ASSURED YOU CAN GET NO BETTER ELEMENT
