
N0. 51 SETTING UNDERWING NOZZLE PRESSURE APRIL 2000
In 51 GamGrams spread over 25 years, we have never addressed this subject directly. It is complex, and often misunderstood. One reason is that there are so many different designs of trucks and hydrant carts. It has taken 2 years to get this GamGram "right"; we hope you agree. We'd like to specially thank ES (you know who you are) for his help on this, really cutting through the complexity.
Please read GamGrams 32 and 33 before reading this one. They contain the background you need to fully understand this GamGram.
THE BASICS
1. Refueling with incorrect nozzle pressures is always a problem. Too much pressure can damage the aircraft.
Too little pressure· refueling takes too much time.
2. The gauge on your vehicle marked "Nozzle Pressure" does not read actual nozzle pressure. It reads
simulated nozzle pressure • see GamGram #32.
3. Actual nozzle pressure depends on several factors: the setting and design of your equipment, aircraft type,
the number of aircraft tanks open, and much more.
4. It is a standard world-wide practice (and specified by the ATA) to have two methods of controlling nozzle
pressure, one is primary and the other is the backup, or secondary. Except when dual hose end regulators are
used, the secondary pressure is 5 • 1 0 psi higher than the primary, or surging will occur as the two controls
"fight" each other.
DESIGN TYPES • We list here the most common basic designs.
1. Low pressure systems, typically low flow rate cabinets and small refueling trucks. These systems are simply
incapable of excessive pressure, but only if a low pressure pump is used.

2. Double Hose End Regulator (HER) Systems. These systems have a deadman control on the main delivery system, but no pressure control. The only pressure control is two hose end regulators on the nozzle. This is inexpensive and reliable, but the nozzle is large and heavy. There is no simple way to tell if the HERs are working correctly.
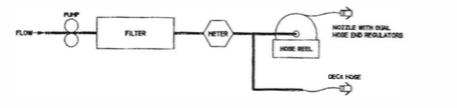
3. Single HER systems have a single pressure control on the delivery equipment, and an HER on the nozzle.Most commonly the HER is the primary control. In some cases, such as on hydrant carts, there may be a pit pressure control valve and inline valve on the ca and an HER on the nozzle. There is no simple way to tell if the HER is working correctly. On a system with a long hose, a HER may simply se e as a surge protection.
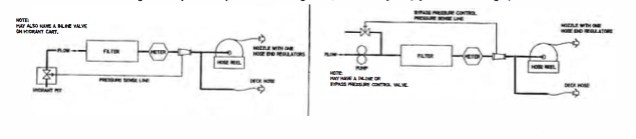
4. Bypass and Inline Valve refueler trucks have the two controls on the truck. This type of system can deliver
the highest flow rate to the aircraft, when properly adjusted. In some cases, a HER may be added as an
emergency backup, but is not necessary if the truck is properly adjusted.
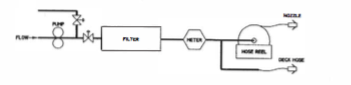
The Super Simple method of setting nozzle pressure (For illustration only, follow your complete procedure to test all your safety systems - follow your company policy!)
1. Connect the refueler or hydrant cart nozzle to a recirculation connection or test stand (NOT an aircraft)
2. Disable the primary pressure control
A. On HER systems; use a block-out device..
B. On ''air set" systems, record and then increase the primary air reference pressure to 90 psi, or if so
equipped, disconnect the venturi sense line QD from the primary pressure control servo.
C. On spring set systems, unscrew the primary pressure control adjuster until loose or if so equipped,
disconnect the venturi sense line QD from the prima pressure control servo.
3. Close a valve downstream of the nozzle slowly. The actual nozzle pressure at any flow rate should not exceed your standard, typically 45 psi. If it is incorrect, adjust the secondary control or repair the secondary .. HER if equipped with dual HERs.
4. On systems with venturi compensators, close the valve slowly again and check to make sure the "Nozzle Pressure" gauge on the refueling equipment matches the actual nozzle pressure. If not, adjust the venturi needle valve to make these pressure match. Repeat step 3 and 4 to confirm proper settings.
5. Enable the primary pressure control. Close the valve downstream of the nozzle slowly. The actual nozzle pressure at any flow rate should not exceed your standard, typically 40 psi. If it is incorrect, adjust the primary control or repair the primary HER if equipped with dual HERs.
6. On systems with venturi compensators, recheck as in step 4 to confirm that the venturi is adjusted to cause the "Nozzle Pressure" gauge to match the actual nozzle pressure.
7. Done!
NOTES:
1. Surging may be caused by air trapped in the pressure sense lines. It can also be caused by trying to set the
primary and secondary pressures too closely together.
2. Test the deadman and emergency stop systems at various flow rates to confirm proper operation.
3. In "Air Set" systems, the air reference pressure is higher than the fueling pressure. For example, a valve with a 16 psi "bias" pressure will regulate at 40 psi when the air reference is 56 psi, 16 psi above the desired fuel pressure. The bias may also be 25 psi.
4. Under no condition should the actual nozzle pressure exceed the "Nozzle Pressure" gauge on your
equipment. At no time should the nozzle pressure exceed your established maximum, and certainly never
exceed 55 psi.
5. Also make sure you do not exceed the maximum flow rate of the filter and meter at any time. This may be controlled by a rate of flow control pilot on the in-line valve.
6. In some cases, the venturi may not be able to provide enough compensation, even if the needle valve is screwed in all the way. In such a situation the actual nozzle pressure at high flow rates will be lower than shown on the "nozzle pressure" gauge on the vehicle. See note 4, do not adjust the pressure too high, change to a venturi correctly selected to use on your system.
7. If you must change a hose length or diameter, you MUST reset your venturi.
Conclusion:
If you properly set up your fueling equipment, you will fuel aircraft quickly and safely.
